A common problem related to the use of silicone elastomers is outgassing of unreacted volatiles. The compounds that outgas can coat surfaces, contaminate processes, or leach into adjacent fluid streams. An accepted method to minimize these escaping volatiles is to apply an extended curing process to the elastomer. Once the volatiles have been removed from the elastomer, they no longer create any problems for the end user.
Post-curing is a process that removes the volatiles from the elastomer by diffusion and evaporation by exposing the part to a temperature greater than its service temperature. Advanced post-curing also involves exposing the component to a vacuum. Once the volatiles are ‘vaporized’ they are no longer available to outgas. If the volatiles are not removed from the elastomer and then exposed to elevated temperatures with poor ventilation, one can expect a reduction in strength, elongation, and compression set properties accompanied by chemical decomposition. The main issue with an extended curing process using heat is the significant amount of time (often days) at required elevated temperatures, which consumes significant amounts of energy and is generally an expensive process.
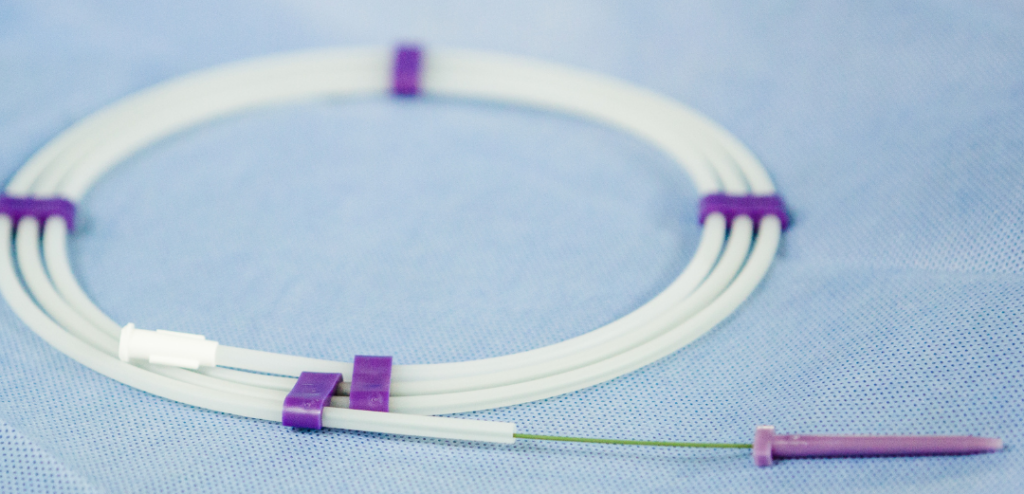
Cool Clean Technologies develops the Enertia™ centrifugal immersion CO2 cleaning system to successfully extract volatiles from silicones and other elastomers. The process is done at room temperature and involves exposing the elastomer component to Liquid Carbon Dioxide (LCO2) under carefully controlled conditions. LCO2 is non-toxic, non-flammable, non-corrosive, odorless, chemically stable, and acquired from recycled sources (it does not contribute to global emissions of CO2).
LCO2 has several characteristics that makes it ideal for removing volatiles from various elastomers:
Affinity for silicones and other volatile components
Easily diffuses into porous elastomeric structures
Very low surface tension
As a result, when the elastomer is exposed to LCO2, it first penetrates and solubilizes un-cured and non-crosslinked compounds, forming a solution which diffuses out of the elastomeric matrix and into the bulk of the chamber. Studies have shown that this process does not materially change most elastomers and has advantages over traditional bake-out and vacuum bake-out alternatives.
The Enertia™ outgassing system is completely automated and very easy to use. After the products are inserted in the chamber and the start button is pressed, the system gently introduces LCO2 into the chamber, controls the process parameters and exposure time, and has a programmed pressure reduction scheme to safely reduce the pressure. Upon completion, the door can be opened and the parts are ready for use or additional processes. Because the Enertia™ equipment is virtually a closed system, operators are able to recover 95-99% of the CO2 for additional extraction cycles.
Typical operating costs – including CO2, electricity, and process heat – range from $10 – $50 per cycle. Specific examples of LCO2 extraction applications are presented below.
Extraction of Food/Medical Grade Silicone
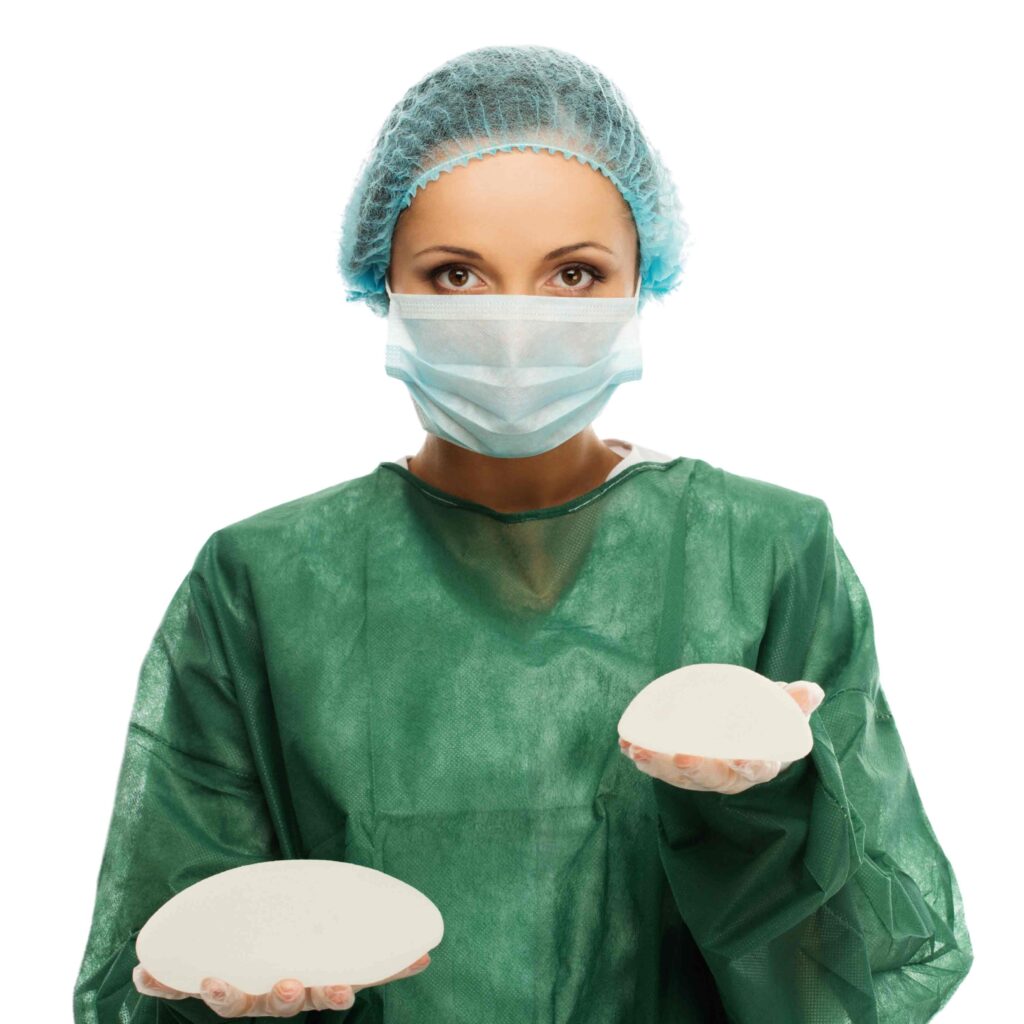
To meet the requirements of food grade and medical grade silicone, the process requires about 50 minutes to remove the volatiles to below 0.5%. or more demanding applications, requiring very low out gassing levels, it is possible to reduce the content of volatiles even further: the amount of cyclic siloxanes D4-D20 can be reduced to below 0.005% (50ppm). In addition, the Enertia™ process can extract volatiles from two component-molded products – silicone and thermoplastic materials. A specific example applied to a medical device product involves the Enertia™ process used to extract free silicone monomers from breast implants. This method replaced an IPA wash system / vacuum bake-out process lasting 16 hours in duration. The Enertia™ method reduced the
processing by over an order of magnitude and yielded a payback of less than 18 months. Another example relates to silicone residue removal from Septa Discs used for life science. The method involved a vacuum bake-out process lasting 30 hours in duration. The CO2-based silicone extraction process reduced the cycle time by 70%, reduced utilities costs by 50%, and yielded better extraction results.
Gamma Sterilization
With the Enertia™ process, the common re-polymerization effect experienced on silicone parts with the use of heat curing will not take place, which means no slit or cut-healing will occur with this new process. For medical devices, the Enertia™ process has demonstrated that it prevents slit-healing of silicone during gamma sterilization. It has long been known that exposure to gamma radiation changes the chemical structure of silicone rubber. Free radicals are formed by the cleavage of chemical bonds in the methyl groups attached to the silicon atoms in the polymer. These radicals combine to form cross-links in a manner comparable to a vulcanized reaction. These cross-links may occur between the tangent surfaces of the incised slit and cause the slit to close, creating a seal that will no longer provide a fluid path.

Outgassing of Aerospace Components
LCO2 based extraction process have been used for years to replace expensive and time consuming traditional vacuum bake-out procedures:
- Outgassing of thermally conductive gaskets
- Reduced TML (total mass loss) from 1.2% to 0.15% in a 30-minute extraction
- Meets outgassing standard by a factor of 6
- Superior to traditional vacuum bake-out procedure lasting 24-48 hours
- Removal of phthalate ester from heater tape
- Reduced TML from 0.7% to 0.04% in a 180-minute extraction’
- Superior to traditional vacuum bake-out procedure lasting 24 – 72 hrs
- Removal of amides and esters from polyurethane foam
- Reduced VCM (volatile condensable material) from 0.025% to 0.006% in a 60 minute extraction;
- Superior to traditional vacuum bake-out procedure lasting 24 – 72 hrs
- Extraction of high temperature silicone rubber
- Reduced VCM from 0.05% to 0.01%
- Extraction of cable assemblies
- Extract volatiles, condensables, and remove particulate matter
- An alternative to solvent wash / wipe followed by vacuum bake-out
- Reduced outgassing time by half in 2-4 extraction procedure
- No impact on electrical characteristics (continuity, isolation, dielectric strength)
- Elastomer Outgassing
- Alternative to traditional vacuum bake-out which requires 100’s of hours
- 4-hr LCO2 extraction process reduced acceptable bake-out target by 100 hrs.