CO2 spray technology offers unique particle and organic residue removal benefits.
Requirements of component cleanliness are constantly increasing and the automotive industry is no stranger to these stringent guidelines. Improper cleaning can lead to expensive rejects, labor intensive re-work, and restrictions in functionality. High level standards for cleanliness of components in the automotive industry has introduced new alternatives to improve the cleaning process for pretreatments, finishes, varnishes, and coatings.
Carbon dioxide (CO2) based spray technologies have been successfully implemented to meet these requirements, along with other precision cleaning and surface preparation applications. CO2 spray cleaning is a waterless solution adaptable to various shapes and sizes of parts, including, but not limited to bumpers, dashboards, head lamps, spoilers, and other interior and exterior parts.
CO2 spray cleaning uses solid CO2 particles, or dry ice, to remove particulate matter and organic material from critical surfaces.The CO2 particles mix with a heated and pressure-regulated inert propellant to form a non-condensing mixture. This integrated spray allows for both controllable spray composition (particle size and density) and energy.
Primary cleaning performance comes from the solid particles of CO2 that are focused at the surface. The CO2 particles sublime upon contact, leaving behind no residue or waste. Because the spray cleans without condensation, no special component heating or cleaning zone segregation is necessary, making the technology easily adaptable to the sort of open-celled cleaning applications used by automotive OEMs.
Advantages over Traditional Systems
Besides the technical capabilities of CO2 spray cleaning for automotive components, there are substantial cost and operational benefits. Traditional paint line cleaning systems consist of multi-stage conveyors of spray washers, typically three and five stages followed by a water rinse. This is followed by a conveyor tunnel drying system laid out in a serpentine manner. These wash lines can be over 100-metre-long, and drying time can take up to 30 minutes. On top of that there are additional operational costs to factor into the process including:
– Electricity to run blowers for drying and power washers
– Heat for drying ovens
– Inlet and outlet water treatment costs
– Consumables (detergents, filters, etc.)
CO2 spray cleaning on the other hand requires less equipment, as there is no need for drying the parts after cleaning. A typical CO2 spray system consists of one or more compact cleaning modules (Omega), a pneumatic booster (AMP), nozzles and robot(s). The figure below illustrates the general layout from the CO2 source all the way to the cleaning application.
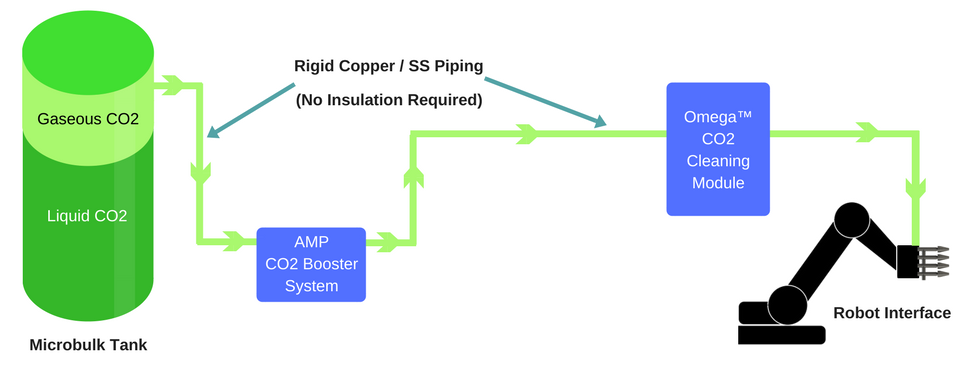